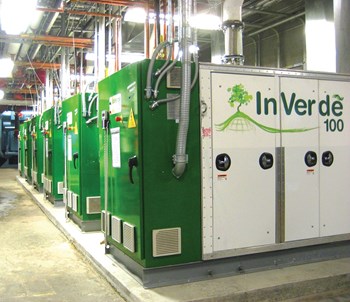
Many residential properties obtain their power from a local energy supplier. But in recent years, boards and managing agents have investigated, and in some cases, installed “cogeneration” systems that allow properties to produce a portion of the energy they use on-site. Like most technologies, there are both benefits and drawbacks to converting to a cogeneration system.
Another term for cogeneration is ‘CHP,’ or “combined heating and power,” and Joseph Gehret of national retailer Tecogen, a designer of packaged combined heat and power equipment, advocates for its use in multifamily markets, including South Florida. “I think that it may be the majority of our market right now,” he says. “They’ve a tremendous use for both heat and electric energy pretty continuously throughout the year, because there’s always a demand for domestic hot water, and they use a lot of electricity for elevators, common area lighting and the like. Our products also have the ability to act as a standby generator, so, whenever there’s a power outage, the common area lights and elevators and water pumps and those types of things continue to operate. This gives boards and residence some level of insurance that they can continue to function.”
Why Cogen?
William Cristofaro, a licensed engineer and president of Energy Concepts, which has offices in New York and New Jersey, explains that cogeneration is the simultaneous production of electric power and HVAC from a fuel-fired engine or turbine. In New York City, for example, he says most buildings have either natural gas-fired engines or small turbines.
“By installing a cogeneration system, condos and co-ops can substantially reduce their energy use, upgrade aged central plant infrastructure, and obtain a source of standby power when the utility goes down,” says Cristofaro. “Often the cogeneration plant project can include other upgrades, such as new boilers and chillers. The energy savings pays for the project.”
The cogeneration movement is not new, and in fact dates back to the early 1980s, explains Vishnu Barran, sales manager for Ener-G Rudox, an East Rutherford, New Jersey– based cogen company that Barran notes installed its first cogeneration system in 1984.
“The demand for energy is ever-growing while it is becoming increasingly expensive. Businesses and individuals are seeking to reduce their costs and carbon footprint,” says Barran. “Cogeneration is highly energy efficient. It can deliver a number of positive financial and environmental benefits, as well as supply an organization with power and heat.”
Whereas cogeneration had its share of skeptics early on, Barran says the movement is trending upward, thanks to “lots of financial incentives” from governmental agencies across the country. “Wherever there are high electricity rates, it is becoming popular,” says Barran. “We are seeing increases in the Northeast, California and Florida.”
Supplementing Power
Cogeneration systems supply the same power and services a local utility does, explains Cristofaro. “These services include electricity, hot water, steam domestic hot water and chilled water,” he says.
Herbert Hirschfeld, a New York licensed engineer and facilities services consultant with decades of experience with cogeneration systems, agrees with the benefits outlined by Cristofaro, but adds that condo and HOA boards must have a full understanding of what a cogeneration implementation project involves before moving forward.
“The vast majority of buildings that adopt a cogeneration system will still be on the grid and dependent on the [local] utility to supplement the building’s electrical requirements,” says Hirschfeld. “From a theoretical point of view, cogeneration is interesting and attractive because you’re consuming one type of energy, but producing two types of energy.”
In co-ops and condos, Hirschfeld explains that the building’s energy is divided into two parts: residential units and common areas – roughly 75 percent and 25 percent, respectively, of the building’s energy consumption. A master-metered building’s total energy load, he explains, is available to a cogeneration system, while a cogeneration system in a direct metered building can only use the energy load from the common areas.
“Cogeneration, generally speaking, is not economically viable in a directly-metered building because the load available to the cogeneration system is not sufficient to make the investment cost-effective,” Hirschfeld says. “So to make a building totally available to cogeneration, it has to be master-metered.”
Plugging In
As Hirschfeld notes, there are a number of criteria a board must consider when determining if a cogeneration system will be a good fit for their community. And while there are incentives from governmental agencies, as Barran notes, flipping this “new” power switch should be done judiciously.
“Installing a cogeneration system is a construction project that is mainly confined to the existing mechanical spaces in the building like the basement, but sometimes some equipment is also on the roof,” says Cristofaro. “There is little interference with occupied spaces.”
To better illustrate the benefits of a cogeneration system, Cristofaro describes a recent project, a 275-unit luxury high-rise co-op in New York City that was built in 1965. The original boiler and steam-fired chiller were nearing the end of their respective useful lives, and the board was faced with a quandary: replace the system at a significant expense, with an estimated 10 percent energy use reduction rate, or invest in a CHP system?
The co-op board decided to adopt a cogeneration system that included a 300-kilowatt CHP plant, seven small gas boilers, two new hot water absorption chillers, sophisticated digital controls, and new pumps. The prior year’s fuel and electricity cost was $1,127,000. After the cogeneration system was operational, the year-over cost dropped by 40 percent, to $674,050.
“Every site is a bit different. It’s just a matter of savings and benefits verses cost,” says Cristofaro. “In the above case, the building got a completely new boiler and chiller plant, which was paid for by the energy savings the building realized.”
In Barran’s experience, a cogeneration system can save a building between 25 percent and 50 percent on its energy costs. And, he explains, a cogeneration system can serve ancillary power needs as well, which many residents have learned during major weather events like Superstorm Sandy and Hurricane Irene, when power was lost across broad swaths of the country.
“One of the additional benefits of a synchronous cogeneration unit is its ability to operate in the event of an electrical utility failure,” says Barran. “Natural gas cogeneration can provide a proportion of standby power [in the event of a utility failure] by operating in ‘island mode’ and providing electricity, heating and cooling to your facility.”
If a building does opt for a cogeneration system, it will have to determine a plan of action with its utility company, which can include navigating direct or master metering issues, administrative and legal concerns as well as HVAC service contracts.
“There are some standard interconnection contracts and methods that are used in [different utility territories],” says Cristofaro. “We work through that as part of our engineering services.”
Moving Forward
If a board is interested in installing and running a cogeneration system, the first step is to confer with the managing agent, explains Cristofaro. As a team, the next step should include soliciting information and advice from proven professionals in the field.
“Boards should speak to professional engineering firms with experience designing and implementing cogeneration plants,” he says. “It’s really important to get an objective and impartial evaluation first. At Energy Concepts, for example, we take the client through the entire process: economic evaluation, grants, design and competitive bidding on hard scope, construction review and commission. Then we help them manage the plant over the years.”
According to Barran, the management of the cogeneration system is critical. He likens the cogeneration engine to a car engine running 17 hours a day, or 217,000 miles per year.
“CHP systems require regular, periodic maintenance and inspection,” he notes. “The unit will require a service after a predetermined amount of hours. Units typically require between six and 10 services annually, depending upon operation. The service procedures vary throughout the year, from replacing and re-calibrating components to oil and filter changes.”
Installing a cogeneration requires both a short-term and long-term view, says Cristofaro. To this end, boards and residents have to consider the overall investment and construction time against the long-term reduction of monthly maintenance and utility costs.
“Savings can vary, but reduction of electric bills by 85 percent is not uncommon,” says Cristofaro. “This figure is offset against the finance payments for the project. Net result is savings for the residents and/or cash put towards a co-ops or condos reserve fund every month.”
W. B. King is a freelance writer and regular contributor to The South Florida Cooperator.
Leave a Comment