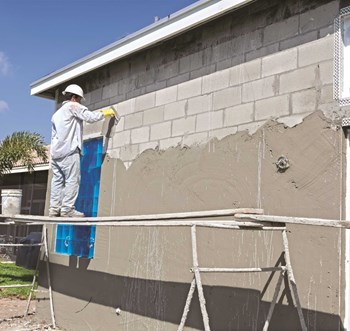
Southern Florida's homeowner associations may not have to deal with much in the way of snow and ice when it comes to protecting and repairing their concrete and stucco surfaces, but they certainly aren't off the hook just because blizzards don't often happen in the Sunbelt.
Tough as they may look, concrete and stucco exteriors need regular care and maintenance. Failing to maintain and repair them can result in unsightly conditions, reduced value, and costly repairs down the road.
Concrete Facts
Concrete and stucco have been used as building materials for hundreds of years, says Mike Rhodes, owner of Homestead Paving in Miami. Conventional or non-structural concrete is used for sidewalks, curbs, and pavements. Anything that is vertical, or spans across columns, is structural concrete, and is composed of different base materials suited for the particular job being done.
By contrast, stucco is a surface treatment that is applied wet to a building's exterior (often over an underlying concrete structure) and hardens to a very dense solid. It is used as decorative coating for walls and ceilings and as a sculptural and artistic material in architecture.
According to Colin Meneely, president of the Southeast Florida chapter of the International Concrete Repair Institute (ICRI) in Pompano Beach, there are a multitude of additives and coatings available to help both materials remain sound and stand up to the elements, including specialized anti-corrosion coatings for reinforcement bars and corrosion inhibitors that can be added directly to the concrete mixture at the plant. “There are also thousands of coatings that can be applied to the concrete after it has been placed to enhance the performance, appearance, and life span,” he says. “A design professional should always be consulted to determine the proper product for the application.”
“We usually don’t have any problems with freezing and thawing in South Florida,” says Gerard Moulzolf, vice president and branch manager for American Engineering Testing Inc. in Bonita Springs and one of the directors of ICRI. “So concrete strength and durability are not as critical as say, in Minnesota.”
That said, there are still certain specifications structural concrete and similar materials must meet in order to be fit for construction purposes. According to Diep Tu, director of engineering for the Florida Concrete & Products Association in Orlando, house or condo building foundations are typically made of 3,500 PSI concrete, while for pavements that support traffic, the industry recommends 4,000 PSI, notes. “Anything beyond 4,000 PSI would get into structural concrete,” he says.
Either way, according to Rhodes, “Maintenance starts at the construction stage. If you don’t get it right at construction, you can’t do a lot about maintenance later on. Once it starts to break up, you have to replace it.”
Keeping it Together
As in most cases, your association's first line of defense against bigger concrete and/or stucco-related problems is its own maintenance staff. According to Raymond O'Steen, owner of O'Steen & Company, a general contractor in Miami, “Traditional cementitious stucco needs to be pressure-cleaned or sandblasted, with any loose material removed and any faults, cracks or openings repaired with a similar material. Then it should be sealed, primed and waterproofed. For exterior surfaces, waterproofing is really the key—much more so than painting. Paint is the lowest level of protection available for an exterior masonry stucco finish. Water migrates through paint finishes—it's not waterproof. Water that does make it through stucco finishes is very deteriorating. At minimum, coating and general appearance inspection should be done about every 24 months.”
According to Mariann Gerwig of Carousel Development & Restoration Inc. in Delray Beach, “There are some signs of deterioration that can be found by a simple visual inspection performed by maintenance personnel and managers. Outward signs include rust spots, cracks, exposed reinforcing bars, loose concrete and falling concrete or stucco.” Any new cracks should be noted during regular inspections. See how the cracks compare over time. Some may not open up further or continue to deteriorate visibly but that does not mean they can be ignored, adds Rhodes. “Once cracks start to develop the surfaces will break up eventually.”
And sometimes the problem goes much deeper—and isn't as apparent to the casual observer. “When moisture penetrates the concrete, it causes the rebar to rust,” Gerwig says. “As rebar rusts, it expands up to seven times its original thickness and exerts a force of over 10,000 psi that causes large cracks. Seemingly insignificant problems on a building’s surface may be outward indications of much more serious problems beneath that can only be determined by a qualified, experienced structural engineer.” Gerwig suggest that HOAs bring in a licensed structural engineer to perform an in-depth inspection of their buildings every few years.
And keep track of what you find, advises Tu. “Keeping good inspection records will allow the owner or management team to take care of potential problems before it becomes an expensive item,” he says. “Our recommendation is for owners and management organizations to budget a certain amount annually [for concrete repairs], do a visual inspection, and perhaps benchmark and see how quickly an area deteriorates to come up with their own maintenance program.”
If a problem exists that is beyond the capability of your staff to repair, it's time to call in the specialists. Generally, that involves first a structural engineer who will do a deep inspection of the problem – as well as the surrounding structure—to get a full picture of the situation and what will be needed to correct it. As with any project big or small, choosing the right professional for the job is crucial, says Gerwig. “It is important that the engineer recognizes his/her responsibility to the association, but also that he or she has a track record of dealing fairly and honestly with restoration contractors, and has a staff adequate to provide timely inspections and meetings as required without causing delays.”
The chosen engineer will survey the building and provide an estimated budget for the work based on estimated quantities of repairs. They will then prepare and administer a bid package to solicit bids for the estimated scope of work to qualified contractors. According to Gerwig, they will also provide signed and sealed specifications required for the permit, direct the contractor where to make the repairs and mark those areas, inspect the repairs as they are being carried out, as well as after the repair is completed. The engineer also issues inspection letters and issues a final inspection letter to the building department stating that all work was completed as specified.
“While the engineer’s opinions are important,” says Gerwig, “it is ultimately the board of directors who hire—and must get along with - the contractor. The board of directors should review each of the contractor’s complete and detailed bids. Analysis of the bids should be predicated not only on price but also on the reputation, financial strength and a successful history of [similar projects].”
If your structural concrete or exterior stucco is in need of care, the pros agree that any contractor your HOA hires should be an American Concrete Institute Certified Flatwork Finisher. These finishers offer concrete construction knowledge, skills, and equipment to get the job done right, as well as guidelines. ICRI standards are written into all specifications. “Look to see how long a contractor has been in business, and possibly look at similar, recent jobs they have completed,” says Tu.
Getting Quality
Like with anything else, there are good contractors and bad ones, and in this day and age when condo and co-op communities are so focused on the bottom line, it may be tempting to go the cheap route. Unfortunately, that approach can wind up costing you.
“Structural concrete restoration is a unique area of construction that has become more common in Florida as buildings begin to age,” says Gerwig. “This is a very specialized area of construction that requires special equipment, materials, processes and procedures, and management. Not only is the work specialized, but the contracts, billing formats, and warranties that apply in general construction simply do not work very well for concrete restoration projects. Over the years, the cooperation of community association boards of directors, managers, general contractors, structural engineers, and construction attorneys has resulted in a body of documents, contracts, and specifications that are commonly used today in concrete restoration.”
The pros also suggest that if budgeting is a concern (and when is it not?) your contractor may be able to develop a maintenance plan to get the necessary work done while staying within budget. Some may be willing to prioritize phases of the project and do them on a sectional basis, bit by bit. The key to success in an approach like this is maintaining a good business relationship with a good contractor. Assuming you’re happy with the work, continuing with the same contractor will keep the level of work – and prices - consistent. It also means the contractor will be familiar with your particular property, which is always an advantage.
Tough as they may seem, concrete and stucco have their vulnerabilities – taking the time to care for them and invest in their protection will not only extend the useful life of these materials, but it will save your association money and hassle down the road.
Hannah Fons is associate editor of The South Florida Cooperator. Editorial Assistant Maggie Puniewska contributed to this article.
Comments
Leave a Comment