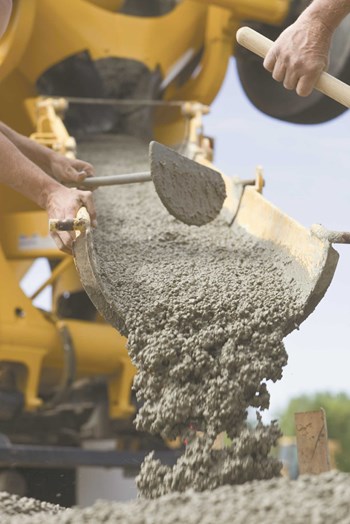
Florida does not have the harsh winters of the north, where thawing and freezing take their toll on concrete. But corrosion of concrete is an issue in South Florida, and homeowner associations need to ensure that the concrete making up their sidewalks, pavements and parking lots, as well as walkways and balconies, is properly installed and maintained.
Some Concrete Facts
Concrete is a mixture of four basic components: rock, sand, cement and water. A concrete mixture is similar to cake mixes, says Diep Tu, director of engineering for the Florida Concrete & Products Association in Orlando. “You can go down a supermarket aisle and see many different recipes. With concrete mixture, it depends on the application of where it is being used.”
“If you are looking for a product that can handle heavier car or truck traffic, concrete is the best product,” Tu continues. While the concrete mixture of the four components has not changed in recent years, new formulations have improved the performance, appearance, and life span of concrete and pavements.
“Chemical companies like BASF are finding the science to prolong the life of concrete,” says Tree Tietsort, president of the Southwest Florida chapter of the International Concrete Repair Institute (ICRI). “Some chemicals are mixed in and some are put on top of the concrete.”
According to Colin Meneely, president of the Southeast Florida chapter of the International Concrete Repair Institute (ICRI) in Pompano Beach, there are specialized anti-corrosion rebar coatings and corrosion inhibitors that can be added directly to the concrete mixture at the plant. “There are thousands of coatings that can be applied to the concrete after it has been placed to enhance the performance, appearance, and life span,” he says. “A design professional should always be consulted to determine the proper product for the application.”
“There are shrinking reducers that minimize shrinking and the potential for cracking,” adds Mike Rhodes, owner of Homestead Paving in Miami. “There are additives for consolidation. The additives used are dependent on the project and the environmental circumstance.”
Concrete, Then and Now
Concrete has been around for hundreds of years, Rhodes said. Conventional or non-structural concrete is used for sidewalks, curbs, and pavements. Anything that is vertical, or spans across columns, is structural concrete.
Portland cement, a pervious concrete mixture, which has been used for more than 30 years, has recently gained momentum based on its ability to handle storm water runoff, says Tu. Pervious concrete mixture is similar to conventional concrete but without the sand, and according to Tu, it resembles a rice krispie treat. “Due to a lack of sand, the mixture creates voids, which allow storm water or water to drain through it or be stored within the pavement,” he says. “So you can shrink the size of the pond and have more available land for future development or parking spaces. If you have any trees or gardening, you don’t have to worry about them. Water and air are allowed through the pavement to the root systems.” Any local ready-mix concrete manufacturer can produce pervious concrete, Tu says.
In addition to pervious concrete and conventional concrete, there are tons of mixed designs, Tu explains. “With each mix you can change anything, from how quickly it sets up and is cured, to its strength.”
Concrete parking lots are designed based on anticipated vehicular loads, volumes and soil condition. Concrete pavement thickness can range from 4.5 to 7 inches. “We usually don’t have any problems with freezing and thawing in South Florida,” says Gerard Moulzolf, vice president and branch manager for American Engineering Testing Inc. in Bonita Springs and one of the directors of ICRI. “So concrete strength and durability are not as critical as say, in Minnesota.”
The contractor or designer specifies the strength of the concrete, such as 1,500 psi (pounds per square inch) for curbs or landscape borders, and up to 2,500 psi typically for sidewalks, stoops, or patios.
For house foundations or condo building foundations, one would typically need 3,500 psi concrete, and for pavements that support traffic, the industry recommends 4,000 psi, Tu notes. “Anything beyond 4,000 psi would get into structural concrete.”
The owner or developer should require the contractor to be an American Concrete Institute Certified Flatwork Finisher. These finishers offer concrete construction knowledge, skills, and equipment to get the job done right, as well as guidelines. ICRI standards are written into all specifications. “Look to see how long a contractor has been in business, and possibly look at similar, recent jobs they have completed,” says Tu.
Caring for Concrete
According to Rhodes, “Maintenance starts at the construction stage. If you don’t get it right at construction, you can’t do a lot about maintenance later on. Once it starts to break up, you have to replace it.”
The two most common problems or maintenance issues associated with paved surfaces are cracking and spalling, says Meneely. Proper curing methods should be followed to avoid unnecessary shrinkage and cracking, Meneely said. “Proper attention should be paid to the location of the reinforcing steel within the area to be poured to ensure the steel has adequate coverage.”
Cracking can also occur due to a lack of curing. When concrete cures improperly, the material does not gain the strength it should by drying out, says Tu. Concrete hardens because of a chemical reaction—or the hydration process between cement and water. Curing is a process to minimize moisture loss after placement.
Installation mistakes are to blame for the majority of these issues, Rhodes says. “If the concrete has too high a slump or too much water—that is a shortcut. The more water you add, the less strength the concrete will have and the more shrinkage you will have. Concrete strength is determined by a water-to-cement ratio. The lower the ratio, the better the concrete will be. The project engineer typically specifies the ratio.”
When it comes to parking lots, some of the most common problems stem from improper joint spacing during installation, Tu says. “When concrete transitions from its fresh to hardened state, it shrinks. So we have to put control joints in concrete pavements to tell it where to shrink.” Joint spacing is determined by the thickness of the pavement in question. Proper layout of control joints around drainage structures can potentially eliminate the majority of cracking problems, and sealing joints surrounding these structures can help minimize saturation of the soils beneath, he says. Inadequate compaction of backfill material around these structures can also result in loss of support for the pavement above.
Other problems can result when the pavement is too thin for heavy loads such as garbage trucks and other utility vehicles. By contrast, a thicker-than-necessary pavement drives up installation costs. Problems also occur when sections of pavement or sidewalks are heaved out of alignment by tree roots, or damaged by heavy maintenance vehicles. For these reasons, tree growth should be monitored, and sections of sidewalk crossing parking lot entrances should be poured thicker.
Signs of Trouble
The most obvious sign of a deteriorating concrete surface is random cracking. Any new cracks in pavement should be noted during regular inspections. See how the cracks compare over time. Some may not open up further or continue to deteriorate visibly but that does not mean they can be ignored, says Rhodes. “Once cracks start to develop the concrete surfaces will break up eventually.”
Elevated slabs should be waterproofed every five years to prevent the migration of water and chlorides into the concrete, says Meneely. Further maintenance tips include applying concrete sealers, joint caulking to minimize the water intrusion, and pressure- or chemical-washing to clean parking lot surfaces of oils and other corrosives.
“Once you see that a panel has lifted slightly, that should be put into the maintenance program because it will continue to worsen over its service life,” says Tu. “Keeping good inspection records will allow the owner or management team to take care of potential problems before it becomes an expensive item. Our recommendation is for owners and management organizations to budget a certain amount annually [for concrete repairs], do a visual inspection, and perhaps benchmark and see how quickly an area deteriorates to come up with their own maintenance program.”
Municipalities have different specifications for inspections in Florida. The Florida Department of Transportation oversees highways and roads. There are also paid consultants who act as inspectors for properties, says Rhodes.
“It is always someone independent of the contractors,” he continues. “They have their specifications booklet that addresses everything from start to finish. They will first look at your concrete mix design. You submit what the concrete is consisting of and the proper proportions. ”
Legal Considerations
When one section of pavement becomes displaced, it becomes an automatic slip-and-trip hazard. This is of particular concern to buildings and HOAs with elderly residents. “When you get downward deflections of over an inch or two that are not corrected, the trip hazard problem is severe, “ Moulzolf says, “and there are plenty of lawsuits filed as a result.” A fall could also be from a slip or trip caused by wet surface or a crack.
“There is a legal duty on the part of a residential board to maintain their property in reasonably safe condition,” says James L. O’Leary, a personal injury lawyer based in Bonita Springs. Their legal duty is to residents of the building, he said. “If a concrete crack is in a walkway and it is foreseeable that a guest could trip and fall, by operation of law, a legal duty arises to maintain the property in a reasonably safe condition. If someone gets injured on the property, the homeowner’s policy or the building’s policy comes into play. The guest could have a claim and a lawsuit could get filed for negligence in failing to maintain the property in a safe condition.” The contractor may also be liable if there was a construction defect.
Injuries on property can result in civil action filed in the appropriate Florida county against the building ownership. If there is a violation of code it can be used in a civil trial as evidence of negligence.
O’Leary advises building owners to do periodic, reasonable inspections of the premises. “Take any remedial measures that need to be taken—it could be from potholes because of the rain, or a tree whose roots have grown so much that is causing pavement or sidewalks to have elevation changes. That needs to be monitored; if there is a crack in concrete, you should have some cones set up, or some tape put out so no one can trip or fall. In that sense, you are giving them some warning about a potentially dangerous condition.”
Peter Malbin is a freelance writer and a frequent contributor to The South Florida Cooperator.
Leave a Comment